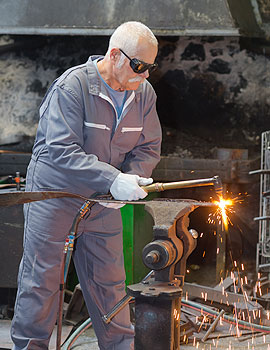
Choosing the right aluminum alloy is crucial for aluminium fabrication companies in Abu Dhabi for successful projects, as different alloys offer varying properties and characteristics suited to specific applications. From strength and corrosion resistance to weldability and formability, understanding the key factors in selecting the appropriate aluminum alloy ensures optimal performance and durability.
Alloy composition:
Aluminum alloys consist of different elements, such as copper, magnesium, silicon, zinc, and manganese, which impart specific properties to the material. The alloy composition determines the alloy’s strength, corrosion resistance, machinability, and weldability. For example, 6061 aluminum alloy is popular for its excellent weldability and formability, making it suitable for a wide range of fabrication applications, including structural components, automotive parts, and consumer goods. Conversely, 7075 aluminum alloy offers higher strength and hardness, making it ideal for aerospace, military, and high-performance applications where durability and toughness are paramount.
Mechanical properties:
Understanding the mechanical properties of aluminum alloys is essential for selecting the right material for your fabrication needs. Key properties to consider include tensile strength, yield strength, elongation, hardness, and fatigue resistance. Different alloys exhibit varying levels of mechanical properties, allowing fabricators to choose the alloy that suits their specific requirements. For example, 3003 aluminum alloy offers good formability and corrosion resistance, making it suitable for sheet metal fabrication, while 5083 aluminum alloy provides high strength and excellent corrosion resistance, making it ideal for marine applications such as boat hulls and structures.
Corrosion resistance:
Corrosion resistance is a critical consideration, especially for applications exposed to harsh environments or corrosive substances. Aluminum alloys are inherently resistant to corrosion due to the formation of a protective oxide layer on their surface. However, certain alloy compositions offer enhanced corrosion resistance, making them suitable for marine, aerospace, and chemical processing applications. Alloys such as 5052, 5086, and 6061 are commonly used in marine environments due to their excellent resistance to saltwater corrosion, while 7075 alloy is preferred for aerospace applications where corrosion resistance is essential for long-term durability.
Weldability and formability:
The weldability and formability of aluminum alloys influence their suitability for fabrication processes such as welding, bending, and shaping. Some alloys are more easily weldable and formable than others, allowing for efficient and cost-effective fabrication of complex components and structures. Alloys with high magnesium content, such as 5000 series alloys, exhibit good weldability and formability, making them suitable for applications requiring intricate designs and tight tolerances. Additionally, alloys with lower magnesium content, such as 1000 series alloys, offer excellent formability and are often used in sheet metal fabrication and automotive applications.